Key Machines
Latest News
Solvent Extraction Plant
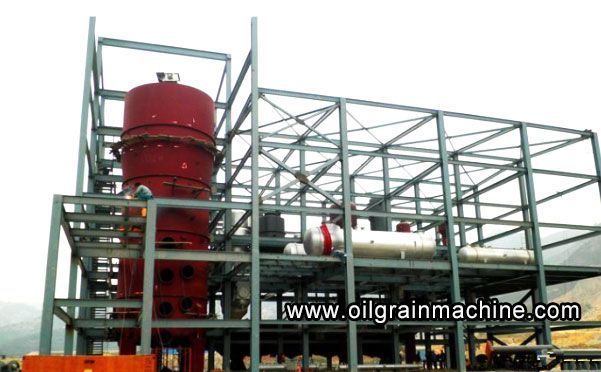
DTDC-Desolventizer Toaster Dryer and Cooler
Desolventizer Toaster Machine
The wet meal dumped by the extractor contains 25%~35% solvent. The desolventizer-toaster is used to recycle the solvent and obtain high-quality finished meal.
DTD serial desolventizer is one of the best equipment of desolventizing in extraction oil plant, and it can finish desolventizing, cooking and drying the extracted meal. Cooperated with steam drying conveyor designed by our company, it can adjust the outlet temperature of meal to meal to 5-10℃ above surrounding temperature and the meal can be packed and stored directly
The wet meal dumped by the extractor contains 25%~35% solvent. The desolventizer-toaster is used to recycle the solvent and obtain high-quality finished meal.
DTD serial desolventizer is one of the best equipment of desolventizing in extraction oil plant, and it can finish desolventizing, cooking and drying the extracted meal. Cooperated with steam drying conveyor designed by our company, it can adjust the outlet temperature of meal to meal to 5-10℃ above surrounding temperature and the meal can be packed and stored directly
We're here to help: Easy ways to get the answers you need.
Product Introduction
DTDC---Desolventizer Toaster Dryer and Cooler
DTD Serial Desolventizer Toaster
Brief Introduction Of Desolventizer Toaster Machine
The wet meal dumped by the extractor contains 25%~35% solvent. The desolventizer-toaster is used to recycle the solvent and obtain high-quality finished meal.
DTD serial desolventizer is one of the best equipment of desolventizing in extraction oil plant, and it can finish desolventizing, cooking and drying the extracted meal. Cooperated with steam drying conveyor designed by our company, it can adjust the outlet temperature of meal to meal to 5-10℃ above surrounding temperature and the meal can be packed and stored directly.
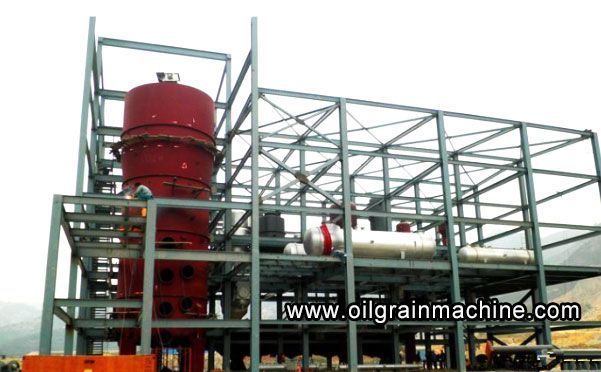
Advantages Of DTDC Desolventizer Toaster
1. Reasonable steam spraying can keep the temperature of vapour phase low at the export of the D.T. And energy consumption also can be reduced greatly.
2. In airtight condition, desolventizing solvent meal effectively and adopting reasonable way to spray direct steam evenly. Compared with traditional desolventizing equipment, this machine can make the residual solvent in meal reach to minimum.
3. In each part of the machine, material particles have the same residence time, so products have high stability and quality.
4. The vapour phase temperature of desolventizer-toaster can be achieved by automatically adjusting the amount of direct steam.
Main Structure And Working Principle
Desolventizer-toaster is made of machine, layer, sieve-board, main axle, scraper, automatic material door, base,driver structure.
Wet meal is sent into desolventizer-toaster by sealed auger, and firstly drops on the heating plate of the first pre-desolventizing layer, then the meal is heated by indirect steam to remove part solvent. With the turning of the paddles, material drops to the next pre-desolventizing layer, then to another. And after three levels, material drops to the main desolventizing layer. There are some direct steam nozzles on the chassis of the layer which can spray direct steam with the pressure of 0.05~0.1MPa, thus the solvent in wet meal can be removed completely. Meanwhile, because of the heat-moisture treatment, the activity of urease in the meal can be ensured within limits. The blanking control mechanism can keep the bed depth at 900~1200mm. After desolventizing, the water content in meal is high, so drying meal with hot air is necessary.
DTD Serial Desolventizer Toaster
Brief Introduction Of Desolventizer Toaster Machine
The wet meal dumped by the extractor contains 25%~35% solvent. The desolventizer-toaster is used to recycle the solvent and obtain high-quality finished meal.
DTD serial desolventizer is one of the best equipment of desolventizing in extraction oil plant, and it can finish desolventizing, cooking and drying the extracted meal. Cooperated with steam drying conveyor designed by our company, it can adjust the outlet temperature of meal to meal to 5-10℃ above surrounding temperature and the meal can be packed and stored directly.
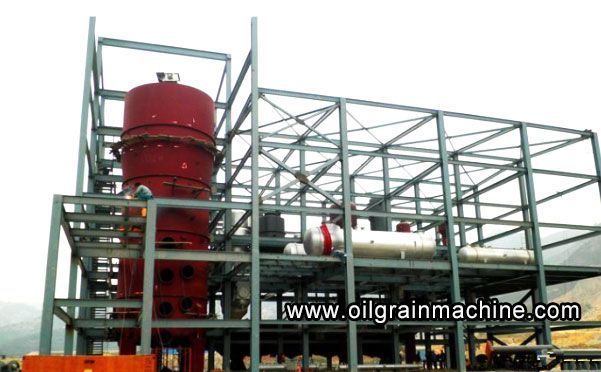
Advantages Of DTDC Desolventizer Toaster
1. Reasonable steam spraying can keep the temperature of vapour phase low at the export of the D.T. And energy consumption also can be reduced greatly.
2. In airtight condition, desolventizing solvent meal effectively and adopting reasonable way to spray direct steam evenly. Compared with traditional desolventizing equipment, this machine can make the residual solvent in meal reach to minimum.
3. In each part of the machine, material particles have the same residence time, so products have high stability and quality.
4. The vapour phase temperature of desolventizer-toaster can be achieved by automatically adjusting the amount of direct steam.
Main Structure And Working Principle
Desolventizer-toaster is made of machine, layer, sieve-board, main axle, scraper, automatic material door, base,driver structure.
Wet meal is sent into desolventizer-toaster by sealed auger, and firstly drops on the heating plate of the first pre-desolventizing layer, then the meal is heated by indirect steam to remove part solvent. With the turning of the paddles, material drops to the next pre-desolventizing layer, then to another. And after three levels, material drops to the main desolventizing layer. There are some direct steam nozzles on the chassis of the layer which can spray direct steam with the pressure of 0.05~0.1MPa, thus the solvent in wet meal can be removed completely. Meanwhile, because of the heat-moisture treatment, the activity of urease in the meal can be ensured within limits. The blanking control mechanism can keep the bed depth at 900~1200mm. After desolventizing, the water content in meal is high, so drying meal with hot air is necessary.
Technical parameters
DTDC-Desolventizer Toaster Dryer and Cooler Parameter
Model | DTD180 | DTD220 | DTD250 | DTD300 | DTD340 | DTD380 | DTD420 | DTD450 | DTD480 |
Capacity (t/d) |
100-150 | 200-250 | 300-350 | 400-450 | 500-600 | 700-800 | 900-1200 | 1500-1800 | 1800-2000 |
Anti-explosion motor (kw) | 30 | 37 | 45 | 55 | 75 | 90 | 110 | 160 | 180 |
Dimension D*H(mm) | Φ2800 x9000 |
Φ3200 x9000 |
Φ3500 x9000 |
Φ4000 x9000 |
Φ4600 x9000 |
Φ5000 x9000 |
Φ5500 x9000 |
Φ6000 x9000 |
Φ6500 x9000 |